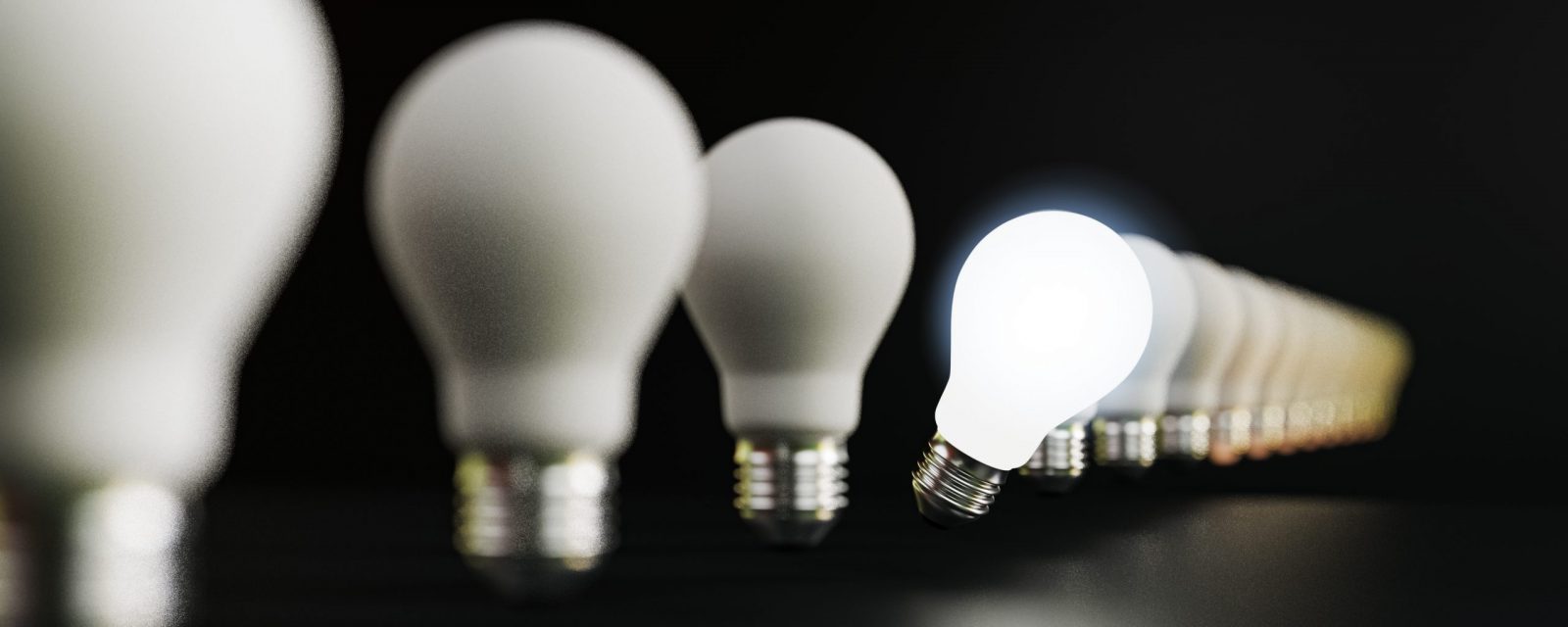
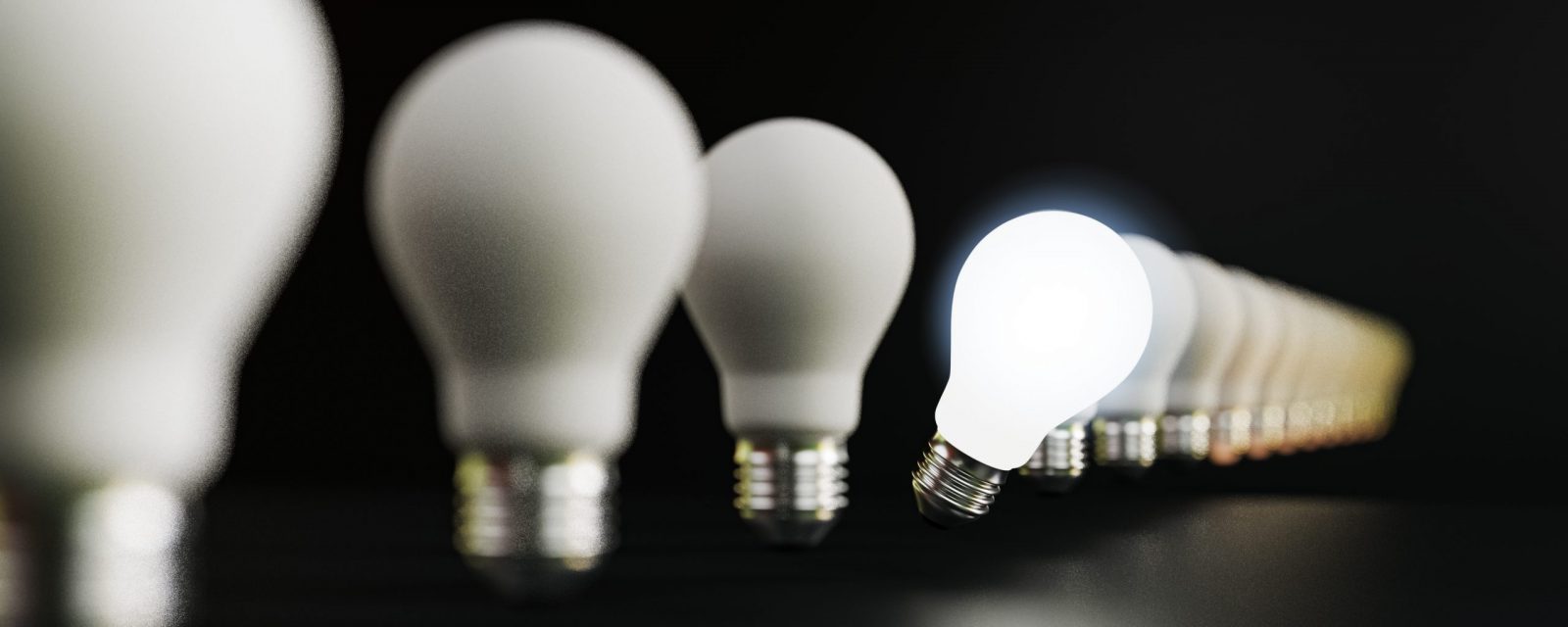
Manufacturing can be grimy work, leaving behind grease, dirt and other material residues that get tracked across floors or spread from one area to the next in the form of handprints, dust and debris.
If you’re a manufacturer working with a so-so janitorial provider, it begins to feel as if a dirty facility is an unavoidable aspect of the work. With no shortage of so-so janitorial providers, too many manufacturers accept a dirty workplace as a necessary status quo. Worse, they end up having to micromanage their cleaning service just to ensure that “so-so” is as bad as it gets.
What happens when sort-of clean becomes acceptable?
At Allegiance Industries, we can assure you: you don’t have to put up with a dirty facility, no matter what you’re making. Your products are not the problem; it’s your cleaning processes.
Don’t Settle for Less than High-Quality Clean
That’s why so many of our manufacturing clients find working with Allegiance Industries something of a revelation: underneath all that dirt and grime? There’s a shiny clean surface just waiting for the right cleaning processes, and a reliable, well-trained team to perform them.
The difference can be night and day as a North Carolina lighting manufacturer discovered after putting up with blackened floors and stairwells for years. A silicon carbide residue left behind by the manufacturing process took the blame that should have fallen on the poor service they were getting from their janitorial service.
Read our case study to see how Allegiance Industries reset the bar for “clean” at the facility and left managers free to do their jobs instead of having to constantly follow up on areas missed by their previous provider.
It’s the difference between a janitorial vendor and a janitorial partner, as one manager described it, and it comes with more than just high-quality cleaning services. There’s also high-quality on-site management and ongoing communication that has allowed the company to completely reset its expectations for clean.
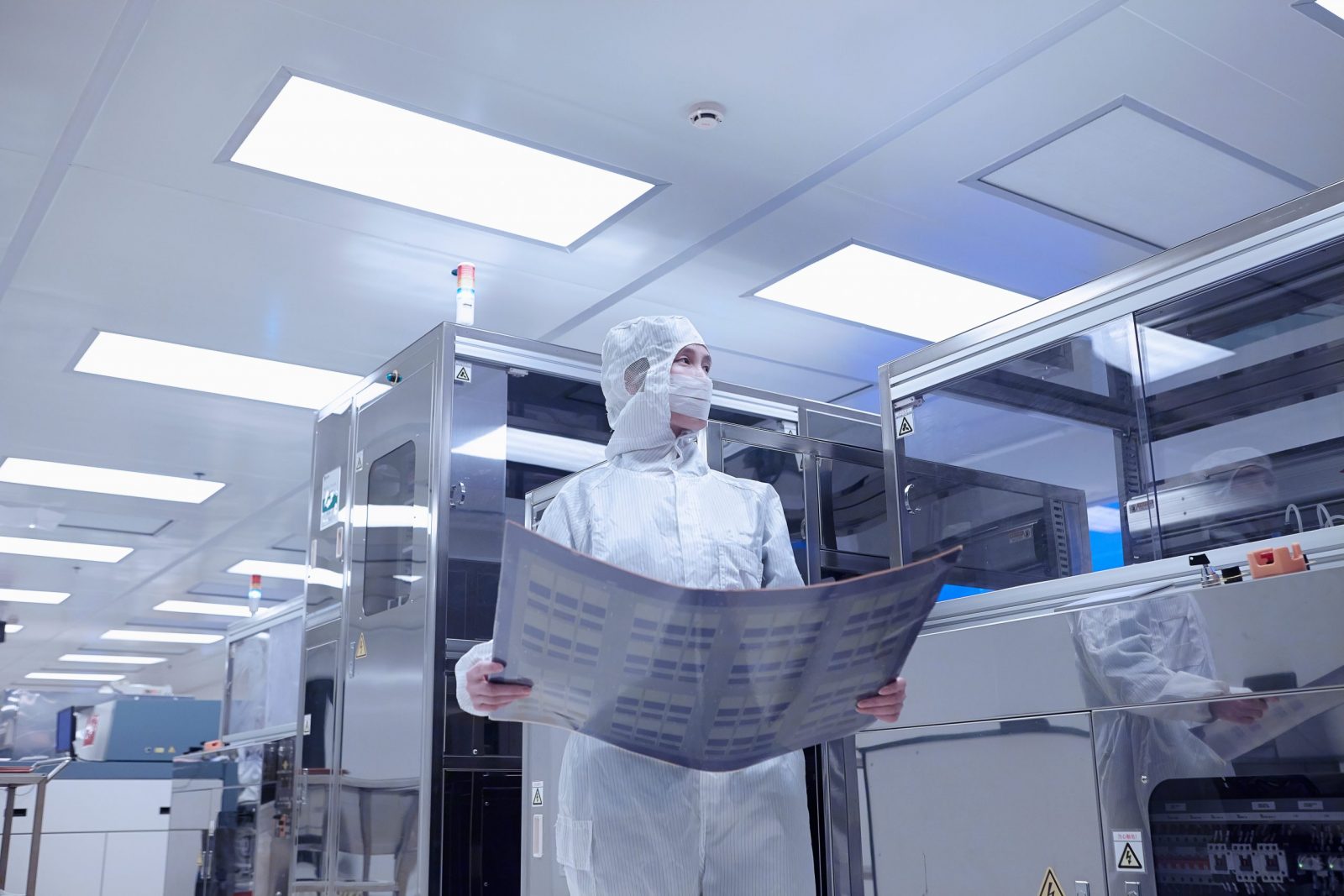
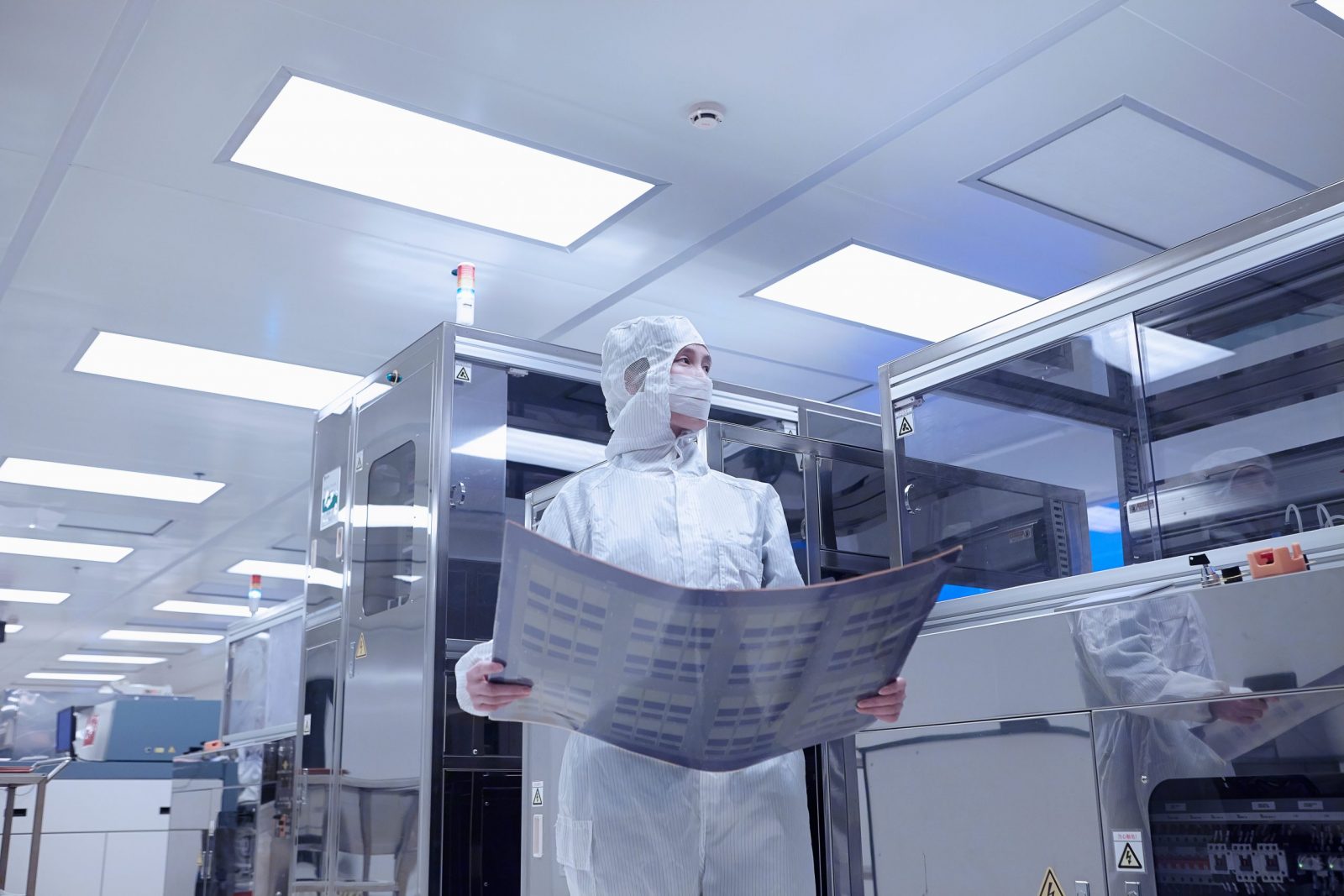
The ROI of High-Quality Janitorial Services for Manufacturing
Raise your expectations and learn the difference that reliable, professional and high-quality janitorial services can make in your facility. From improved employee morale, to time you don’t have to waste checking up on the work you paid for, to the impression you’ll make on your auditors and visitors, it’s clean that comes with a significant ROI.
Read our case study and give us a call to learn about the difference we can make in your manufacturing facility.