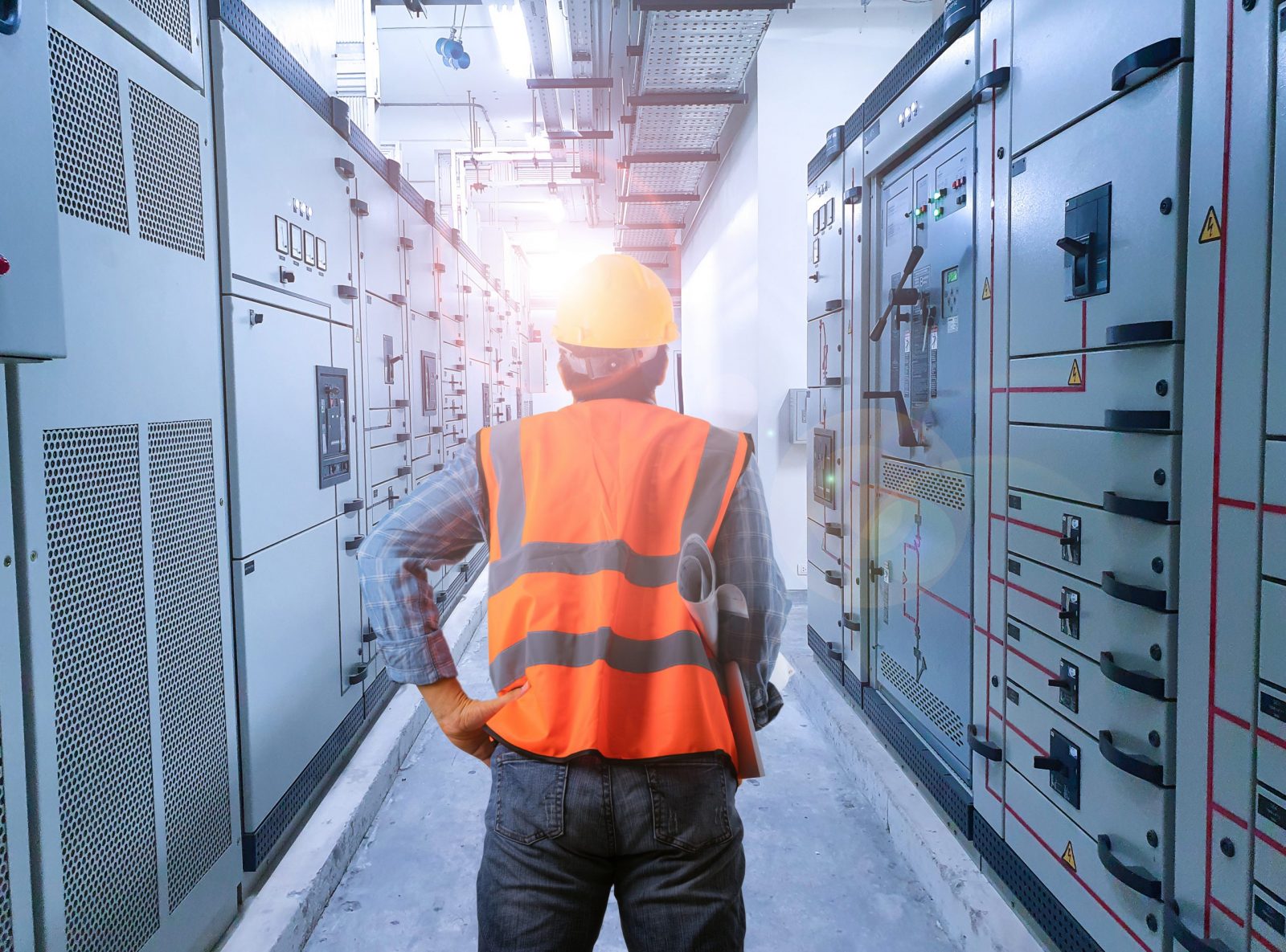
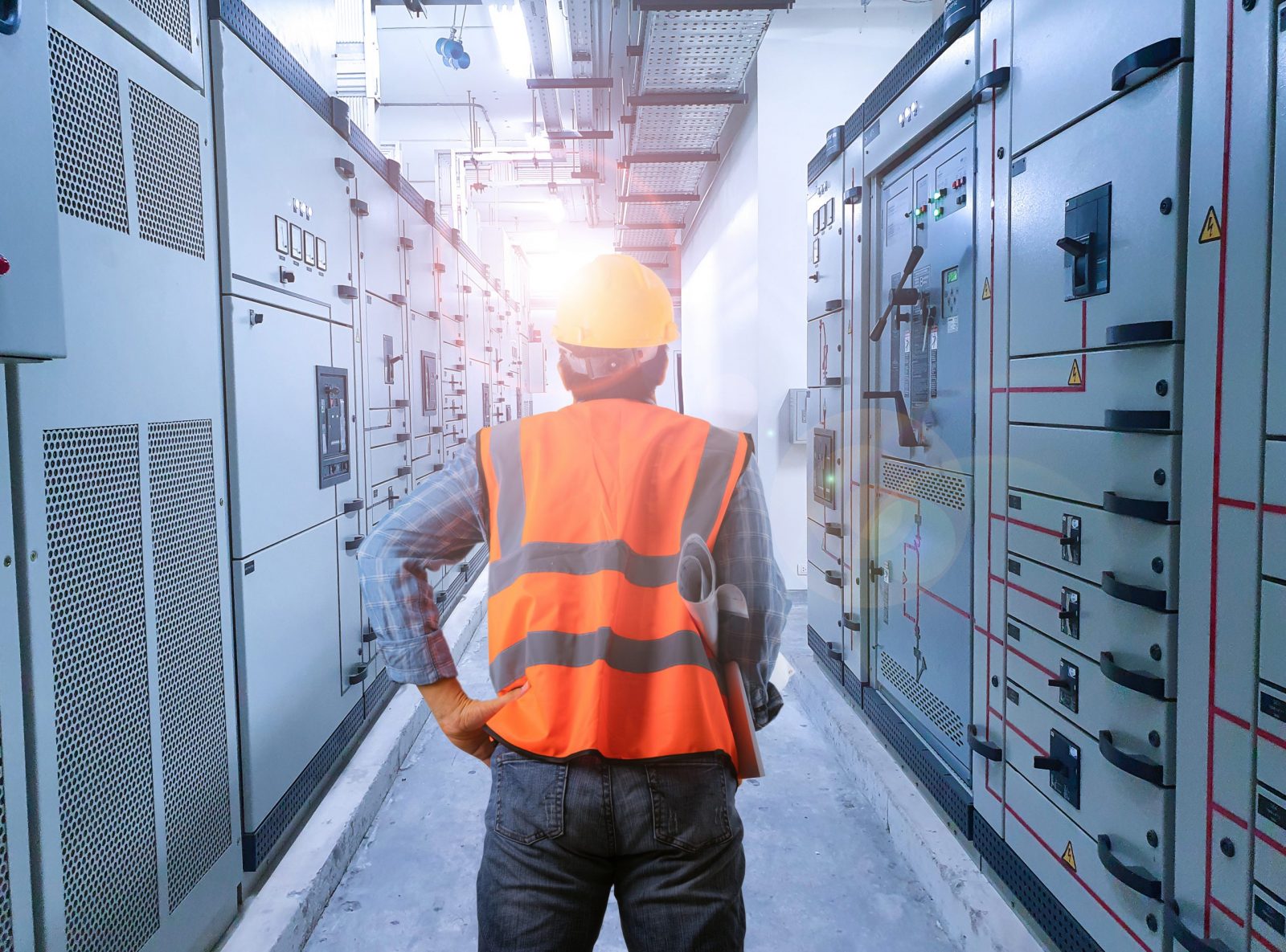
Preventing employee injuries and production downtime starts with these electrical best practices.
Keeping your business and your employees safe, productive and efficient takes a holistic and proactive approach to electrical maintenance. Manufacturers, schools and other organizations do so by commissioning the following best practice evaluations and preventative maintenance from Allegiance industries.
1. Annual Facility & Equipment Review
Electrical safety starts with an annual review of your entire facility, including all electrical channels and equipment. A thorough inspection will locate hot items such as faulty wires and loose connections.
An early diagnosis of potential hazards not only helps to prevent injury, but also prevents costly downtime.
2. Arc-Flash Assessment & Annual Update
An assessment of arc-flash hazards determines an employee’s potential exposure to extreme temperatures, ignition of non-flame resistant clothing, burns, vision loss, and determines the type of personal protective equipment (PPE) necessary for protection. This federally mandated assessment is governed by the Occupational Safety and Health Administration (OSHA) and must be completed each year with updated guidelines posted to every electrical panel in the building.
While safety glasses and a flame-retardant shirt may be sufficient for some panels, others will require full protective gear. An electrical maintenance partner can perform annual or semi-annual updates of your arc-flash assessments to ensure the ongoing safety and compliance of your facilities.
3. Outdated Programmable Logic Controllers (PLCs)
Older commercial buildings often have outdated PLCs and programs with no backup. In the event of program failure, your facilities could lose electricity and require an entire rebuild of the system – along with a substantial chunk of downtime. Newer PLCs are more robust and reliable – a Cadillac system compared to the PLCs of the past.
A professional electrical maintenance partner will evaluate your existing PLCs and create a backup program for a smooth transition. For heavy industrial organizations, manufacturers, and more, backup PLCs can be implemented during yearly shutdowns to avoid unscheduled delays.
4. Annual Electrical Gear Preventive Maintenance
For manufacturing facilities that produce byproducts such as dust, carbon, or wood chips, preventive electrical maintenance keeps gears clean and mechanically sound. Buildup of such material in electrical panels can cause permanent damage if not regularly cleaned, leading to unscheduled shutdowns, and more.
An electrical maintenance partner will thoroughly clean your entire system – from lugs and components to breakers, contractors, and more. Every piece of gear in the electrical cabinet (or room) will be left dust-free and running smoothly.
5. Energy Management Analysis
Without an energy management assessment, organizations risk overpaying for power. Assessing your current energy management includes motor maintenance, control assessment, and replacement of your variable frequency drive (VFD) to prevent shutdowns, extend the life expectancy of motors, and more.
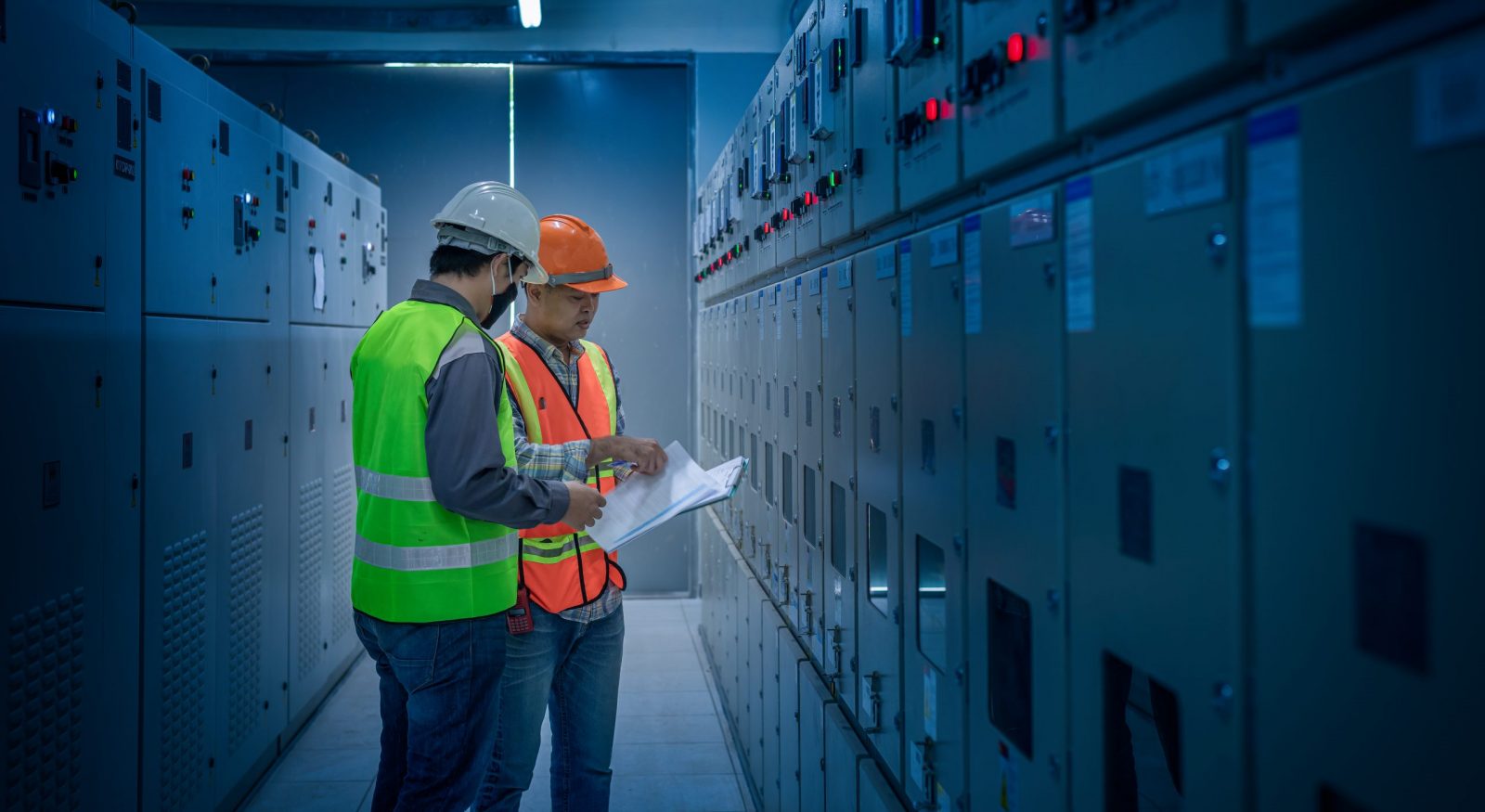
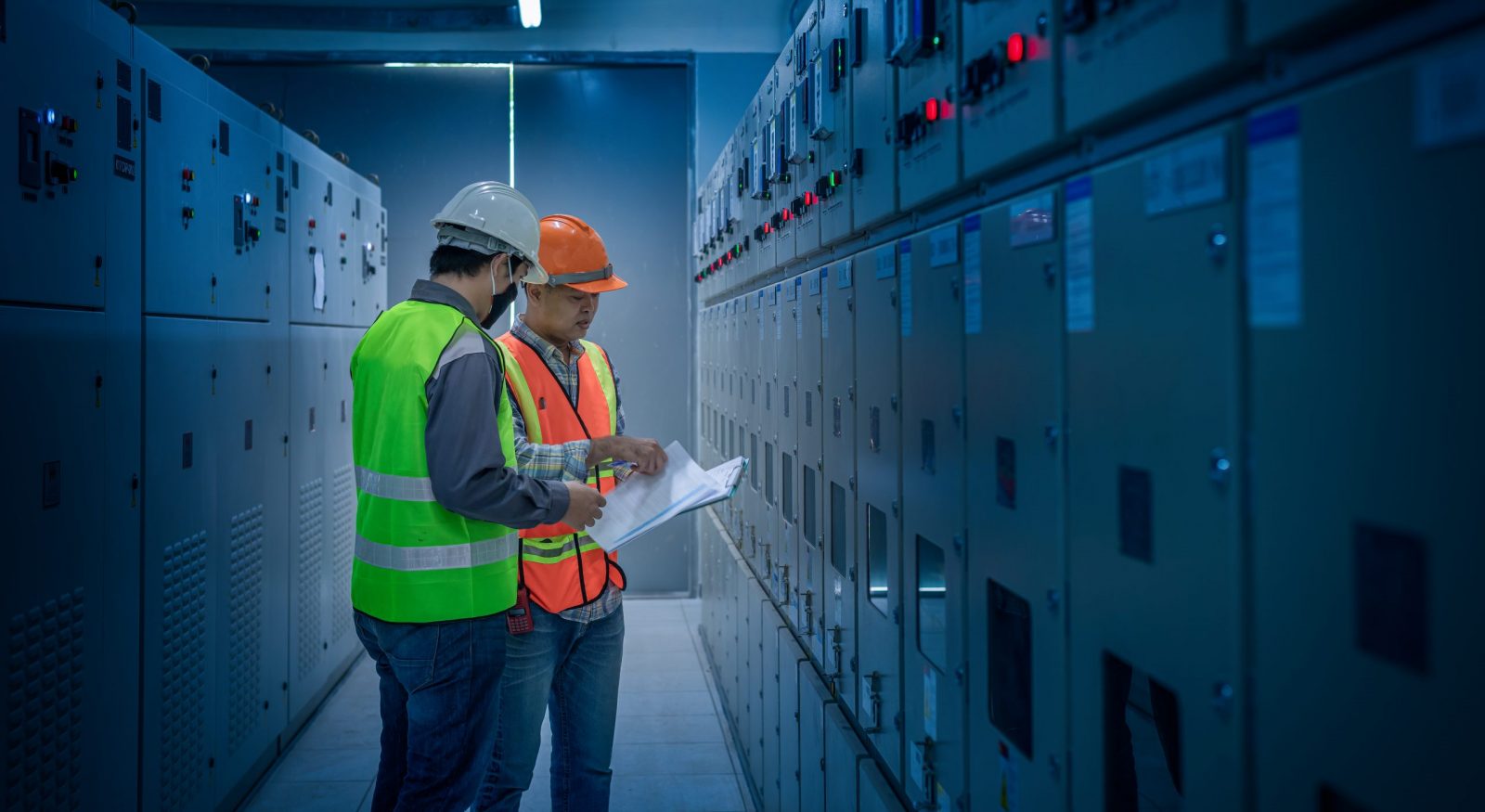
24/7 Electrical Maintenance Services
Allegiance Industries offers around-the-clock electrical services designed to maintain your facility’s energy efficiency and electrical safety. Our teams of highly trained electrical crews are certified to handle a full range of electrical and lighting needs.
From plant maintenance to power supplies and wiring, panel box construction, and more, we offer same-day, emergency, and turnkey solutions for facilities of all sizes and industries. Contact us to learn more about maintaining the safety, integrity and efficiency of your electrical systems.